El control del suministro de material de vía tiene un doble objetivo: por un lado, asegurar que la calidad del material proporcionado corresponde al inicialmente previsto, y por otro, que con el control y la gestión del acopio del material se asegure el cumplimiento de los plazos de la obra. Basta subrayar que en una obra de montaje de vía de alta velocidad, los trabajos estrictamente de montaje de vía suponen aproximadamente el 20% del presupuesto, mientras que los materiales suponen el 80% (20% balasto, 20% traviesas, 20% carril y 20% aparatos de vía). El trabajo de asistencia técnica se centra, por tanto, en dos puntos, la gestión del suministro y el control de la calidad, para lo que se supervisa la producción en la fábrica o cantera, y realizar las verificaciones con ensayos periódicos y recepciones según la normativa vigente.
Hace más de 30 años se comenzó a tejer la red ferroviaria española de alta velocidad, que hoy cuenta con más 3.100 kilómetros en servicio y numerosos tramos en construcción. Entre 1988 y 1990, Ineco empezó a redactar los estudios previos de la línea Madrid-Barcelona y los primeros proyectos constructivos vieron la luz entre 1994 y 1995. Por entonces, el GIF (Gestor de Infraestructuras Ferroviarias) encargó a Tifsa –empresa vinculada a Ineco desde 1999 y con la que se fusionó en 2010– la definición tecnológica de los elementos de la superestructura, un contrato que para Moisés Gilaberte, director de Negocio Ferroviario en Ineco “supuso por volumen e importancia, un hito de especial relevancia. Desde entonces se presta apoyo a la administración en el seguimiento de la producción, planificación y despliegue logístico del suministro a obra y control de calidad de todos los materiales instalados en las líneas de alta velocidad, convirtiéndonos en referente europeo en tecnología de vía”.
Desde que se llevaron a cabo los trabajos en el montaje del tramo de 481 kilómetros entre Madrid, Zaragoza y Lleida, inaugurado en 2003, hasta hoy, Adif Alta Velocidad, con el apoyo de Ineco, ha acumulado una amplia experiencia en organización y control del suministro de los materiales de vía empleados en alta velocidad. La industria española ha sabido adaptarse a unos elevados requisitos de calidad y a plazos de producción y suministro muy exigentes, de manera que, actualmente, es capaz de abastecer las necesidades de construcción de la red de alta velocidad española y, en muchos casos, exportar su producción, como ha sido el caso de parte del material para el AVE entre La Meca y Medina. En España, entre los últimos trabajos en control de calidad de los materiales de vía figuran los tramos de alta velocidad Venta de Baños-Burgos, León-Variante de Pajares-Pola de Lena, Zamora-Pedralba- Ourense, Plasencia-Badajoz, Monforte del Cid-Murcia, Antequera-Granada y Atocha-Torrejón de Velasco.

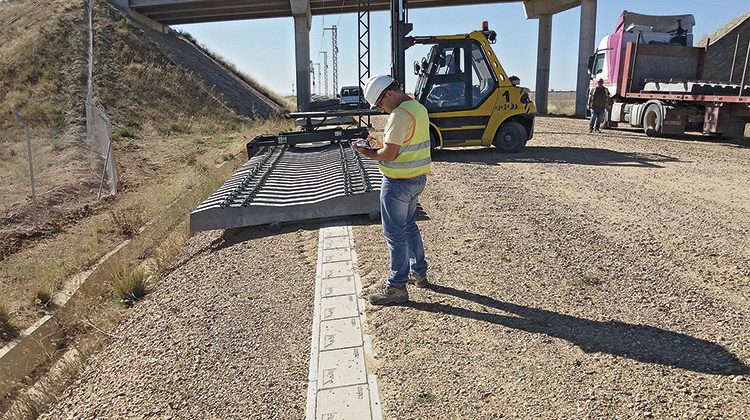
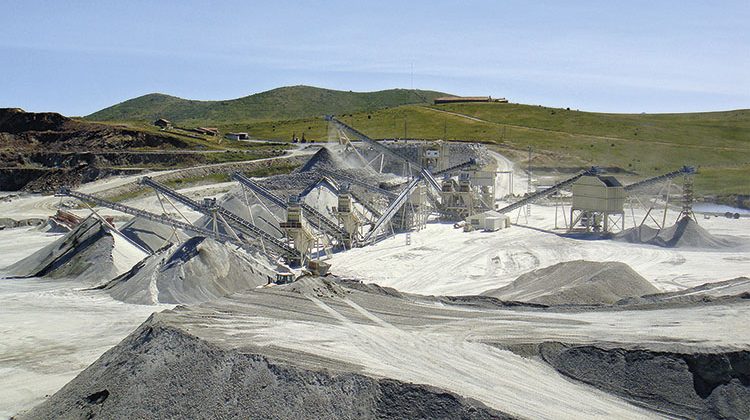
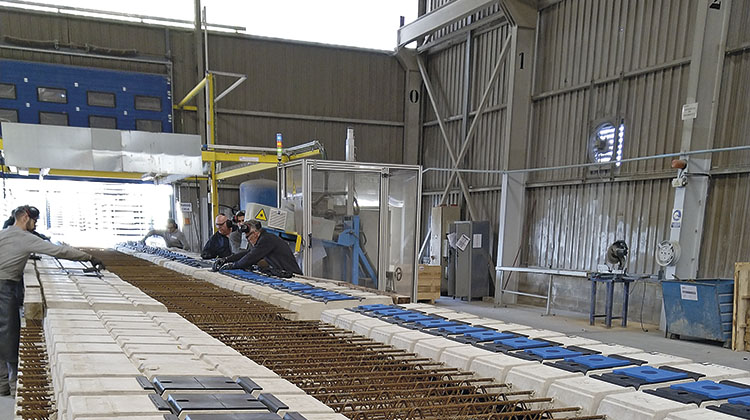
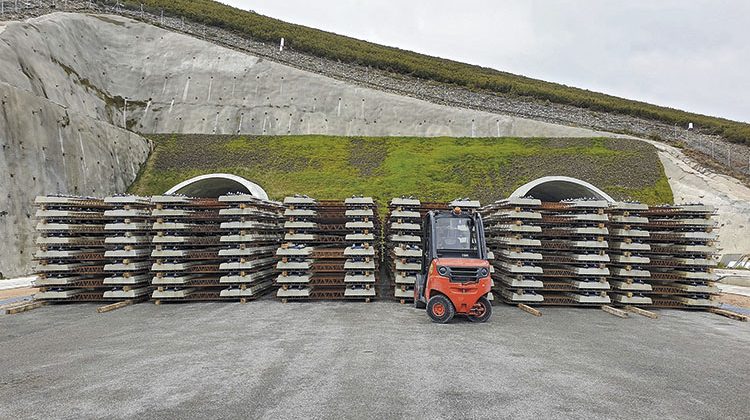
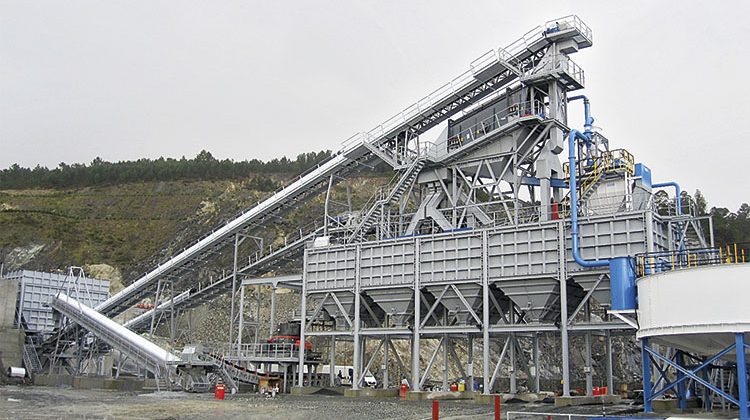
Desde la inspección visual, las mediciones y pesajes, hasta los ensayos de contraste en laboratorio, pasando por el control de las operaciones de montaje hasta las puestas en servicio, las funciones de la asistencia técnica de Ineco incluyen comprobar la adecuación de los materiales a los pliegos de suministro y a la normativa, vigilando la ausencia de defectos tanto en la fabricación, como en las sucesivas etapas de transporte, acopio y puesta en obra. Para ello se identifican los lotes por fecha de fabricación y empresa, de manera que haya una trazabilidad clara, realizándose muestreos que permitan la validación de cada lote en función de las mediciones y ensayos de contraste, garantizando así la calidad del material que se incorpora a las obras.
Por cada uno de los materiales se abre un dosier en el que se incluyen todos los datos (mediciones, ensayos de contraste, etc.), que se entrega a Adif como documentación necesaria para la puesta en servicio de la línea. En el caso de los aparatos de vía, se controlan, además, todas las operaciones de montaje, generándose un protocolo de recepción en vía de cada aparato, documentación también imprescindible para su puesta en servicio. Además, expertos de Ineco asesoran sobre los materiales de vía en las fases de diseño, montaje y explotación.
La vía está constituida por el balasto, las traviesas, el carril y los aparatos de vía. Todos ellos forman la llamada superestructura de vía de alta velocidad, y se ubican encima de la capa de forma.
Durante estos 15 años de colaboración entre técnicos de Ineco y Adif se ha efectuado el control sobre más de 1.100 desvíos y unos 700 aparatos de dilatación
Las piedras del balasto y su milimétrica inspección
El balasto se utiliza desde los inicios del ferrocarril como soporte de las vías férreas, amortigua y reparte las cargas transmitidas al paso de los trenes, asegura la estabilidad de la vía, permite el drenaje de las aguas de lluvia y facilita las operaciones de nivelación y alineación de la vía. Las rocas para la extracción del balasto serán de naturaleza silícea y preferentemente, de origen ígneo o metamórfico. Su granulometría está casi totalmente integrada dentro del tipo grava gruesa, la mayor parte de sus elementos de piedra partida están comprendidos entre los tamices de 31,5 y 50 mm.
Al balasto se le exigen principalmente características relacionadas con su forma y con su dureza de manera que se obtenga una banqueta permeable, pero con gran compacidad y muchas aristas vivas en las partículas que la componen. El objetivo es que se comporte como un lecho elástico pero muy estable. Para ello se busca conseguir el mayor número de contactos entre piedras, lo que unido a la elevada dureza que se exige al material, hace que durante la instalación y la explotación se minimicen roturas y desgastes del material, y consecuentemente se mantenga el mayor tiempo posible la geometría de la superestructura de vía, reduciéndose las operaciones de mantenimiento.
España cuenta con 45 canteras homologadas para la fabricación de balasto tipo 1, que es el utilizado mayoritariamente en toda la red ferroviaria. El control de este material se comienza en la propia cantera, llevando a cabo un plan de muestreo semanal en función de la producción. Por norma general, se realizará un ensayo completo de balasto cada 6.000 t de nueva fabricación. Ineco en colaboración con un laboratorio acreditado por ENAC para la toma y realización de ensayos de balasto, analiza los resultados de un ensayo completo que contiene análisis granulométrico, contenido en partículas finas, contenido en finos, coeficiente de forma, espesor mínimo de los elementos granulares, longitud de las partículas coeficiente de desgaste Los Ángeles y homogeneidad del balasto. Por último, durante el suministro a obra se realizan ensayos de balasto para velar por la calidad y se controla el balasto realmente suministrado con las básculas de pesaje instaladas.
Las dimensiones y colocación de las traviesas
La traviesa se define como un componente transversal de la vía que controla el ancho de vía y transmite las cargas del carril al balasto. Para la construcción de las vías de alta velocidad se emplean traviesas monobloque de hormigón pretensado que utiliza armaduras pretensadas o postesadas para precomprimir el hormigón. Si hacemos referencia a la tipología más utilizada en alta velocidad, el tipo AI-VE, su longitud es de 2.600 mm y la masa mínima sin sujeciones es de 300 kg.
Los trabajos de control de calidad incluyen la recepción en fábrica de las traviesas producidas. De forma resumida, la recepción consiste en la revisión del aspecto externo y de la trazabilidad, verificaciones geométricas que afectan al ancho de vía, verificaciones geométricas de cotas críticas y de cotas principales y los ensayos mecánicos, además de la verificación de los ensayos en laboratorios externos que exige la especificación técnica. Una vez en la obra, es importante planificar el suministro en función del plan de obra para evitar retrasos y sobrantes innecesarios.
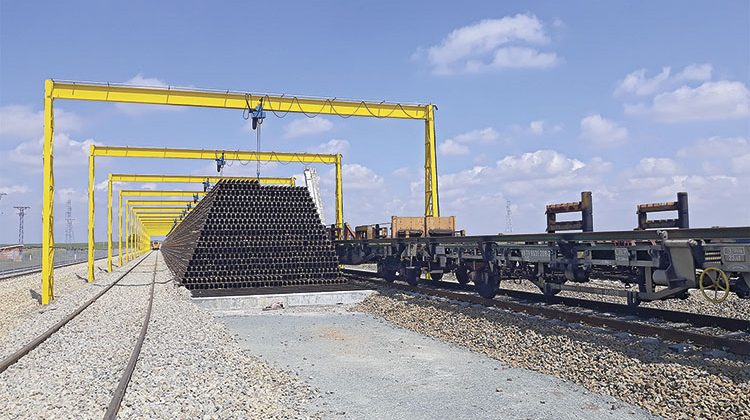
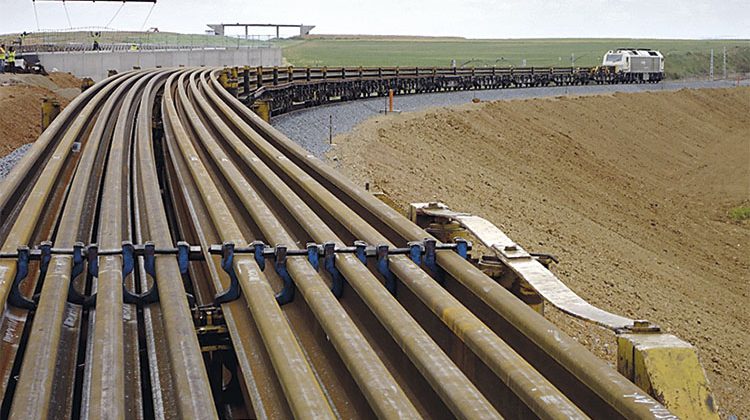
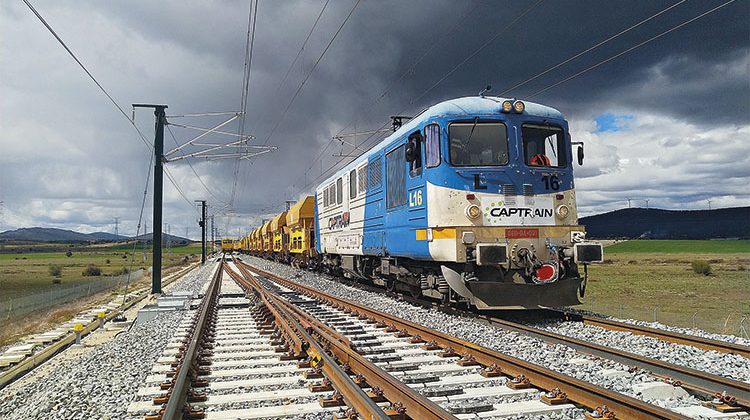
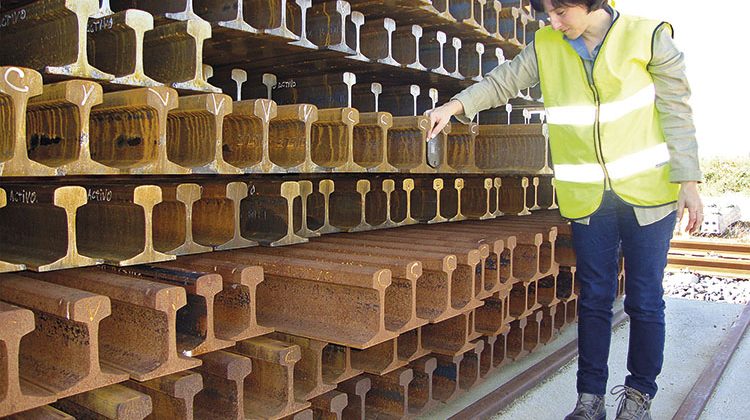
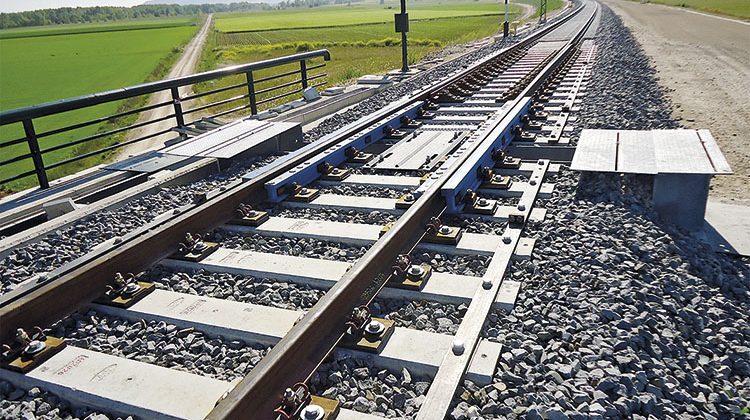
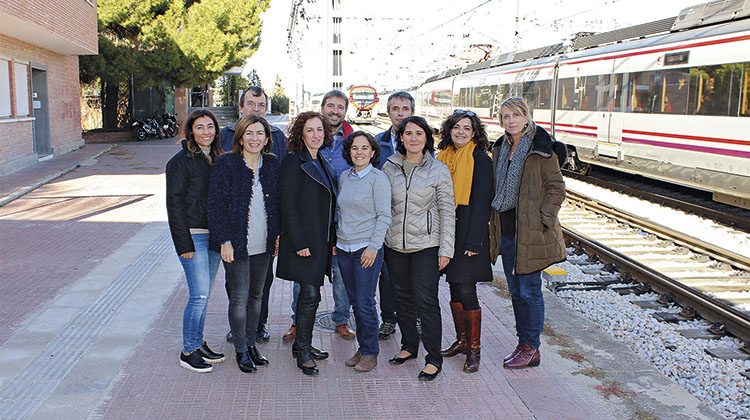
La calidad del carril y la soldadura
Una vez dispuestas las traviesas a lo largo de la traza sobre el lecho de balasto, se procede a la descarga del carril sobre las traviesas desde el tren carrilero, equipado con pórtico para poder realizar la descarga.
El carril como elemento fundamental de la vía, debe contar con una serie de características que le permitan resistir un complejo conjunto de esfuerzos: su perfil, su longitud y su composición metalúrgica deben ajustarse a los requerimientos establecidos en la vía. El carril instalado en las vías de las líneas de alta velocidad española es de perfil 60 E1 y calidad R260, de acuerdo a la normativa europea y según la Especificación Técnica de Adif.
Por lo general, en las vías españolas el carril se monta en barras largas soldadas (288 y 270 m), longitud que ha ido variando en función a la longitud de la barra elemental (36, 72 y 90 m) que la conformaba, por la necesidad de reducir el número de soldaduras, delicadas de realizar correctamente y generalmente con peores características geométricas y mecánicas que el carril, constituyendo puntos de perturbación a la rodadura de los trenes que son necesarios de vigilar en la fase de mantenimiento… Actualmente, la alta velocidad española apuesta por el empleo de barras elementales de 108 m, que posteriormente serán soldadas con soldaduras eléctricas mediante planta móvil. El objetivo es aumentar al máximo la longitud del carril elemental, hacer una soldadura eléctrica con medios automáticos, sin metal de aportación y con la mínima intervención humana, de manera que el producto resultante se asemeje al máximo a una barra laminada de manera continua, tanto por composición como por geometría libre de defectos.
El control de calidad llevado a cabo por Ineco, en lo que respecta al carril, implica por una parte validación en la fábrica del carril (barra elemental) y posteriormente en el taller de soldadura eléctrica (barra larga soldada). Para ello se llevan a cabo las verificaciones de geometría y de las calidades externa e interna de carril y soldadura eléctrica, además de realizar sobre ambos elementos ensayos de contraste en el laboratorio externo.
Previo al suministro del carril, se comprueba junto al fabricante y suministrador el estado de la losa de acopio, su nivelación, así como las instalaciones para la manipulación del carril (pórticos y polipastos). Una vez almacenado el carril en la losa de acopio, se inspecciona su disposición y se realiza una verificación aleatoria de la geometría mediante plantillas pasa/no pasa. Además, Ineco lleva el control de la trazabilidad del carril suministrado a cada línea de alta velocidad, fundamental de cara a poder identificar en el futuro la situación física de barras producto de una misma laminación que, con el paso de los años hubiera podido dar lugar a la aparición de algún defecto no detectado por los controles habituales.
La industria española ha sabido adaptarse a unos elevados requisitos de calidad y a plazos de producción y suministro muy exigentes, abasteciendo las necesidades de construcción de la red de alta velocidad española y en muchos casos exportando su producción
El control de los aparatos de vía
Los aparatos de vía son elementos esenciales para la explotación de la vía férrea ya que en un caso permitirán el paso de una vía a otra –los denominados desvíos– o absorber los movimientos que se producen en los viaductos hiperestáticos debido a diversos factores (dilataciones por temperatura, efectos del frenado, efectos reostáticos, etc.), que son los denominados aparatos de dilatación, que compatibilizan los movimientos de contracción y dilatación por efecto térmico con la superestructura de vía situada encima. En España, existen cuatro empresas que se dedican a la fabricación de los aparatos de vía, (dos en Asturias y dos en el País Vasco) de forma que abastecen la casi totalidad del suministro nacional y una parte representativa del internacional (Arabia, Turquía, Argentina, Brasil, México, etc.)
El número de controles y chequeos son continuos ya que los desvíos que se emplean en las líneas de alta velocidad permiten velocidades de paso de hasta 350 km/h en vía directa y 220, 160, 100 u 80 km/h por desviada, dependiendo de los modelos, por lo que se debe garantizar la seguridad en todo momento. El control de estos aparatos comienza verificando el cumplimiento de los parámetros principales durante el premontaje en taller, labor que se formaliza con la firma de un protocolo de recepción. Asimismo, se comprueban las entregas y los plazos del suministro a obra y, una vez en la base de montaje, se revisan los mismos parámetros antes de incorporar el aparato a la vía.
Cuando la vía se encuentra en primera nivelación, al menos, se pueden incorporar los aparatos de vía. A partir de ahí, se efectúa un control topográfico durante las fases de bateos y estabilizados hasta alcanzar la cota definitiva. Una vez verificados los parámetros topográficos se levanta el acta de aprobación. Posteriormente, se vuelve a revisar el aparato, se comprueba que todos sus elementos están en perfecto estado y que funcionan adecuadamente, controlando por última vez el cumplimiento de los parámetros que garantizan su funcionamiento con completa seguridad. Llegado a este punto se realiza el protocolo de recepción en obra, que formará parte de la documentación que se entrega antes de su puesta en servicio.
En cuanto a los aparatos de dilatación, además de los trabajos descritos, se debe realizar la medición de forma periódica de las juntas de los viaductos para distintos rangos de temperatura. En base a las mediciones junto con la temperatura a la que se tomó, se obtiene una recta de progresión que permite determinar si el aparato de dilatación proyectado es el correcto o si por el contrario es preciso utilizar otro modelo ya que con el proyectado no se aseguran las condiciones de seguridad y el funcionamiento exigido. La dilatada experiencia del personal de Ineco posibilita que se efectúen continuas colaboraciones con los fabricantes de aparatos, para conseguir evolucionar los modelos, mejorar las prestaciones, reducir los costes y sin que esto afecte en lo más mínimo a los estándares de seguridad exigida. Durante estos 15 años de colaboración entre técnicos de Ineco y Adif se ha efectuado el control sobre más de 1.100 desvíos y unos 700 aparatos de dilatación.